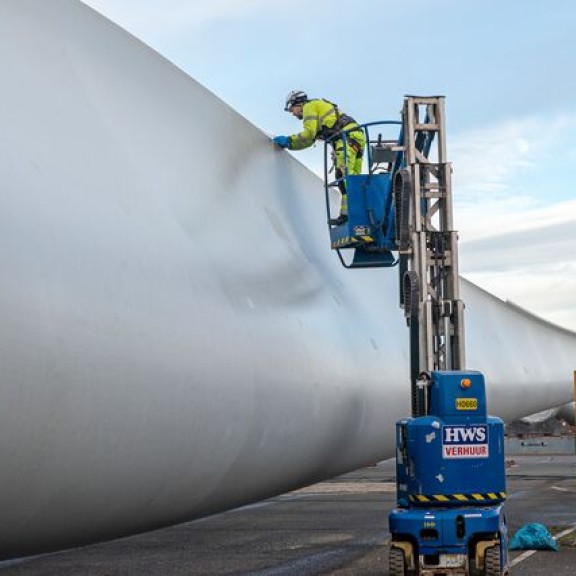
How to make offshore wind circular?
By: Dorothy Winters, programme manager Offshore Wind, Amsterdam IJmuiden Offshore Ports (AYOP)
Offshore wind is one of the fastest growing sectors, with Europe investing some 26 billion euros in wind at sea during 2020 alone. Wind is one of the main components for generating sustainable electricity as part of the energy transition. With the first generation of wind turbines from the period 2007-2008 reaching the end of their lifespan, the sector is facing new challenges with regards to circular decommissioning.
The offshore wind industry is becoming increasingly aware that while it designs, builds and maintains, it was until recently set up in a linear way. In other words, there are no functions for wind turbines after use. James Hallworth, Allard Klinkers (both from Port of Amsterdam) and Dorothy Winters (AYOP) participated in a number of sessions in recent months focused on the sustainability and circularity of wind turbines.
The circular perspective is a broader subject than offshore wind alone of course. Port of Amsterdam and the Amsterdam Metropolitan Region are now considering how the linear approach can be translated into a circular one.
Challenges
The development of circular wind turbines comprises various focal points, three of which are covered in this article: the continuous development of the turbine, the differences between various turbine generations, and challenges related to composite processing.
Fast development
A major demand for wind energy combined with a strong technological development is literally making the turbines grow in height, volume and weight within a substantially price-driven background. The focus is on making everything stronger, lighter in weight, larger and, therefore, more efficient. Circularity has not been sufficiently taken into account.
Multiple generations
There are differences between the various generations of turbines. The materials used in a blade in the first generation were not applied in later ones. This also means that solutions we can apply now to the first generation may not be easily transferable to the second or third generation, and so forth. The first generation of turbines were so ‘battered’ by the saline offshore conditions that their parts are no longer suitable for reuse.
Composite challenge
The blades are made from composite combined with other materials such as wood, fibre, resins and glues; materials that are difficult to separate into individual elements. As the first blades return from sea there are only a few possible applications for reuse, such as reinforcing concrete, placing in playgrounds or as roofing for bicycle sheds. It is important to note that although the volumes of the blades are a significant part of the turbine, they are relatively small for a specific composite processing market on an industrial scale.
What can we learn from other sectors?
Looking at the production, construction and dismantling of offshore wind equipment and the related electrical infrastructure, there is plenty of common ground with other sectors. The production industry, high-tech sector, logistics, maritime, offshore oil & gas, data-driven maintenance, energy and infrastructure; our North Sea Canal region features a wide diversity of industries. So which examples do we see around us that can be applied to offshore wind? And what can we learn from other sectors?
Integrated design
Like cars, wind turbines have a LEGO-like design and include parts from various suppliers. In contrast to electrical plants, for example, the lack of design integration is an issue during the decommissioning process. Manufacturers look almost exclusively at their own components. We believe that exchanging options and opportunities could reap rewards and help avoid dismantling risks. Rather than simply reversing the construction process, things should be set up so that the parts can be reused.
Service concepts
Nowadays, you can lease a car or office lighting, and the batteries of your Tesla remain the property of the builder. New business models are popping up in various sectors such as car sharing or leasing household appliances. Ensuring that a turbine remains the property of the builder or OEM avoids discussions about ownership and who’s responsible for decommissioning.
Reusing parts
On land we see that revised wind turbines find a second life at other locations. When repairs are needed turbine manufacturers just replace the relevant parts. In the aircraft industry, a sector with similarly high standards, there is a market for revised parts – with certification. This means that data-driven maintenance would have benefits during use as well as enabling a proper inventory for an end-of-life turbine.
How can the region contribute?
Our region has a healthy ecosystem for high-quality circular processing within a range of 30 kilometres. The success of this ecosystem relies on various factors: knowledge of materials, experience in reuse and processing, and logistical expertise.
Material expertise
The North Sea Canal region and Amsterdam Metropolitan Region accommodate a broad range of highly technical companies. From the processing of electronics, fibres and end-of-life plastics or composites to environmental expertise, applied research and non-destructive testing, these organisations could play a role in assessing the materials and options for reuse and even function as potential buyers.
Experience & space
Circular activities are already ongoing with sectors such as waste processing becoming increasingly refined. There are many companies with knowledge and expertise related to circularity which they can apply to turbine materials. The potential for our sector lies with a broad number of companies and start-ups that apply these techniques in other sectors, but have yet to enter the offshore wind sector. A decommissioning location in the Amsterdam port would provide the space for these activities.
Logistics
Decommissioning does not revolve around reverse logistics, or dismantling something in the way it was built. The next stage should determine how the dismantling and transportation are set up. Whether a blade is used to provide shelter at a bus stop or for a pyrolysis process to create an oil product defines how the dismantling takes place. Moreover, accommodation and processing within a range of 30 kilometres prevents unnecessary transportation of materials and provides a sustainable option.
Yes we can!
Various members of Amsterdam IJmuiden Offshore Ports are involved in decommissioning oil & gas platforms. It is good (and promising) to see they have already jointly determined that it is feasible to make a circular case commercially successful. And this is Port of Amsterdam’s and Amsterdam IJmuiden Offshore Ports’ aim for offshore wind, too. In a region that represents the entire chain, our knowledge and experience can contribute to smart solutions. Together, we can learn how to expand the applications at the end of a wind turbine’s lifespan and use this as input for designing the front.